Fiberglass Composites Improve Durability of Ports and Marine Structures
Ports are the engine of economic development worldwide and play a key role in the global supply chain. Ports infrastructure needs to be resilient and sustainable to cope with the heavy load demands and aggressive environmental factors. Fiberglass composites are increasingly being used in place of steel and timber to provide increased durability and eradicate the risk of corrosion in steel and rot in timber.
Impact of Corrosion on Ports
Corrosion in concrete infrastructure is caused by salt and brackish water. There are multiple factors that encourage the deterioration of port infrastructure where steel is commonly used including:
- wet and dry cycles from tidal movement. The tidal zone is a highly active area for corrosion activity.
- atmospheric corrosion caused by salt spray and the climate.
- high moisture, chloride, and oxygen exposure.
Concrete is viewed as a natural barrier to chlorides getting to the steel rebar but this ‘solution’ is very short-lived. In any environment, where there are salts, chlorides, water, or chemicals, these will reach the steel rebar over time. In port and coastal environments, this can happen much faster.
Eastland Port upgrade, Gisborne
Why does steel corrode?
When iron oxide (steel) corrodes, it expands by multiple times its original size. When the steel expands it causes stress in the concrete which leads to concrete spalling. Evidence is visible in seawalls, ports, wharves, and other coastal infrastructures worldwide.
Steel and timber (used to a lesser extent as it is prone to rotting) are used in aggressive coastal environments and in doing so, rely on expensive maintenance and upgrades to extend their life cycle. Multiple protection measures are put in place in the form of cathodic protection, protective coatings, and maintenance programs – all to manage the inevitable impacts of corrosion and shortened life cycles. This maintenance is expensive and can be highly disruptive in a busy port under continual pressure to meet shipping and delivery schedules.
Fiberglass composite advantages for port and marine assets
Ports are expanding to cope with the increasing demands of world trade. Engineers are now using turning to GFRP composites to deliver infrastructure that is built to last without relying on maintenance and protective measures. GFRP composites are replacing traditional materials in port and marine structures including:
- concrete deck reinforcement
- quay walls and sea walls
- diaphragm walls
- sub-sea cables and pipelines
- marinas, floating pontoons, and dolphins
- cassions and breakwaters. A recent study: Evaluation and Optimization of the Life Cycle in Maritime Works, shows how using GFRP instead of steel increases the performance of these structures throughout the service life.
What are the benefits of fiberglass composites in port structures?
Ports and other coastal structures can benefit from using GFRP materials. Rotterdam Port (The Netherlands) and Eastland Port (Gisborne, New Zealand) have both invested in fiberglass composites to deliver better durability and reduce the need for disruptive maintenance.
Europe's busiest port uses GFRP composite technology
Rotterdam Port (pictured above) is the oldest and busiest port in Europe. According to Port Economic Management, the port of Rotterdam is 40km long and 10km wide. It accommodates 30,000 oceangoing ships and 130,000 river ships each year. In 2018, the port handled 469 million tons of freight, including 14.5 million Twenty-foot Equivalent Units of container traffic.
These volumes are forecast to increase and the Rotterdam Port Authority is ensuring they have the infrastructure in place to manage this growth. Expansion and optimization of port infrastructure are continuous with a strong focus on safety, sustainability, and performance.
Part of the container port upgrade in Rotterdam included reconstructing the Automatic Guided Vehicles (AGV) pathways. The demands on these concrete slabs are extremely high due to the heavy load work of the AGVs and other loading equipment. Pultron's composite dowels and Mateenbar™ composite rebar were selected as the best materials for this application.
The corrosion-resistant dowel advantage
GFRP composite dowels provide the longest life cycles of all dowels. 184,000 pieces of 38mm composite dowel were supplied for this project to provide these advantages:
- High shear strength – excellent load transfer efficiency
- Corrosion-free – no joint expansion and no maintenance
- Non-electromagnetic – no interference to sensitive electrical equipment
- ¼ weight of steel – faster to install and easier to handle
- Low bond strength – no need to grease dowels.
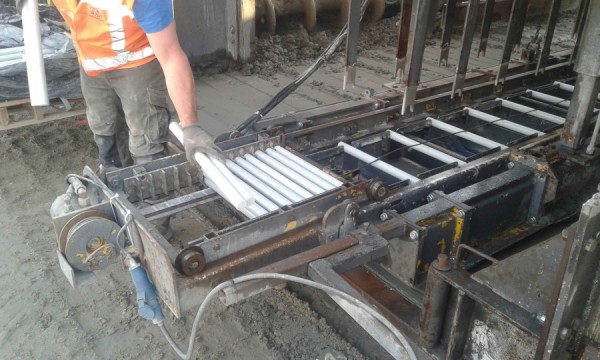
Pultron Dowels used in the Port of Rotterdam
Eastland Port replaces steel and timber with fiberglass composites
Eastland Port is a crucial transport hub for the Gisborne region and one of the biggest logging exporters in New Zealand.
The breakwater repair and breakwater extension project are currently underway as part of the biggest port upgrade in the last 100 years. The impact of corrosion is evident throughout the port with broken concrete and epoxy repair used to mitigate damage – the result of relying on steel and timber in a marine environment. For the new upgrade, steel and wood were replaced with Mateenbar™ as the primary concrete reinforcement.
Advantages of using fiberglass composite rebar in the port upgrade:
- The structures will not corrode, therefore concrete will not spall or break.
- No expensive maintenance and/or repair work.
- Mateenbar™ composite rebar is highly durable with a life cycle of at least 100 years.
- Mateenbar™ is lightweight. It can be easily cut on-site, it's faster to install and less heavy lifting equipment is needed.
- To avoid large-scale rehabilitation measures or expensive corrosion protection measures, fiberglass composites provide a sustainable and long-life solution to improve asset life cycles for marine structures. Life cycle cost and sustainable management can be greatly improved by working with materials that provide strength and durability without the need for maintenance.
To learn more about using fiberglass composites in ports and marine environments, contact us today.